Extrusion
Extruded products account for more than 50% of the European market for aluminium products, of which the building sector accounts for the largest share. Extruded aluminium is used in window and door profile systems in residential and commercial buildings, in housing and prefabricated building structures, in roofing and exterior cladding materials, curtain walling, shop fronts, etc. In addition, extruded aluminium is also used in cargo transportation, in aircraft fuselages, road and rail vehicles, and for marine applications.
The term "extrusion" is often applied to both the process and the product obtained when a hot cylindrical ingot of aluminium (called a billet) is passed through a die with the appropriate shape (direct or forward extrusion, see Figure 1). The resulting profile can be used in long lengths, or can be cut for use in structures, vehicles or components. Extrusion is also used as a raw material for machined bar, forging or cold extrusion products. Although most of the many extrusion presses in the world fall within the simple description given above, it should be noted that some presses can use rectangular ingots to produce extrusions with a wide cross-section. Other presses are designed to move the die along the billet; the latter operation is often referred to as "indirect" extrusion.
The versatility of the process in terms of the number of alloys and shapes possible makes it one of the most valuable elements in enabling the aluminium profile manufacturer to offer customers solutions to their design needs.
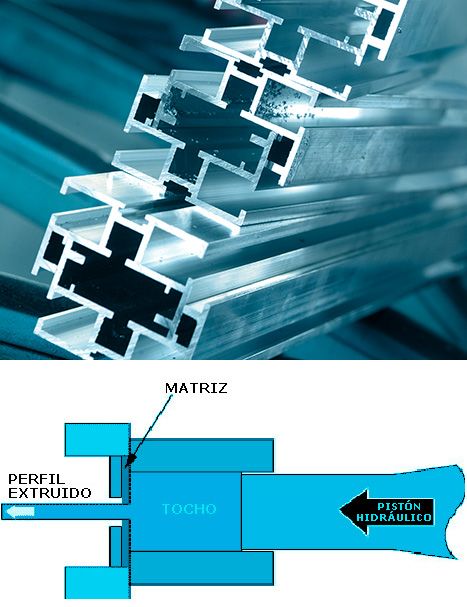
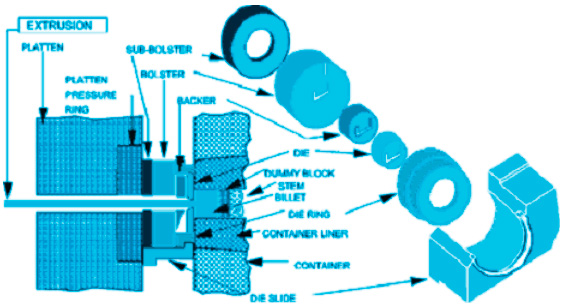
Extrusion process
The key features of the process are as follows: A hot ingot, cut from a long billet (or, for small diameters, from a larger extruded bar), is housed inside a hot container, typically between 450°C and 500°C. At these temperatures, the flow stress of the aluminium alloys is very low, and by applying pressure via a hydraulic piston (ram) the metal flows through a steel die at the other end of the container. This process results in a profile whose cross-section is defined by the shape of the die (see Figure 2)
All aluminium alloys can be extruded, but some are less suitable than others because they require higher pressures, allow only low extrusion speeds and/or have lower surface finish and profile complexity than desired. The term "extrudability" is used to cover all these issues, with pure aluminium on one side of the scale, and strong Aluminium-Zinc-Magnesium-Copper alloys on the other. The 6000 series alloys (Aluminium-Magnesium-Silicon) occupy the lion's share of the extrusion market.
This group of alloys has an attractive combination of properties, important both from a production and usage point of view, and has been the subject of a large number of R&D projects in many countries. This has resulted in a range of materials, with strength between 150 Mpa and 350 Mpa, and all with good toughness and formability. They can be easily extruded and in general, their "extrudability" is good, although those containing magnesium and silicon levels at the lower end of the scale, for example 6060 and 6063, extrude at very high speeds, up to 100 metres per minute, with good surface finish, suitability for anodising and maximum profile cross-sectional complexity together with minimum wall thickness.

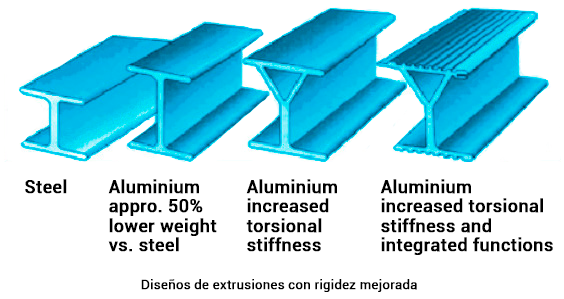
The force applied by the presses varies from a few hundred tonnes to 20,000 tonnes, although most are in the 1,000 to 3,000 tonne range. Extrusion billet diameters range from 50 mm to 500 mm with a length of 2 to 4 times the diameter. Although most presses have cylindrical containers, some have rectangular containers for the production of profiles with wide cross-sections and small thicknesses.
The ease with which aluminium alloys can be extruded into complex shapes makes legitimate the claim that it allows the designer to "put the metal just where it is needed", an important requirement when dealing with a relatively expensive material. Moreover, this flexibility in design makes it easy, in many cases, to overcome the fact that aluminium and its alloys have only one-third the elastic modulus of steel (see Figure 3). Since stiffness depends not only on the elastic modulus but also on the profile geometry, it is possible, by increasing the thickness of an aluminium beam by 1.5 times the thickness of the steel beam it is intended to replace, to obtain the same stiffness of steel with half the weight. In addition, with a little extra cost at the machining stage, features can be added to the profile shape that increase torsional stiffness and add grooves for, for example, fluid removal, cable routing, anti-slip grooves, etc. These features on a steel beam would mean extra costs due to the need for welding and forming, which partly reduces the initial difference between the costs of steel and aluminium.
What is anodising?
Anodising is an oxidation process based on electrolysis that is developed on the aluminium material.
The aluminium layer is developed by immersing the aluminium in a bath of sulphuric acid, and passing a current of approx. 6000 Amps at 20 Volts between the aluminium (the anode) and the cathode. The layer produced is an integral part of the aluminium, not an applied layer. This layer hardens the surface, makes it more resistant to abrasion and improves the metal's resistance to corrosion; the anodic layer further insulates the surface of the aluminium and provides a decorative appearance through a wide range of colours.
The anodising process offers a wide range of applications. Anodising has been used in the building industry for over 60 years. Anodising offers the hardest and safest architectural finish available today. Anodised aluminium is easy to clean and requires little maintenance.
The Qualanod Association has established a set of technical specifications and a Quality Label in order to offer consumers a guarantee for high quality anodising.
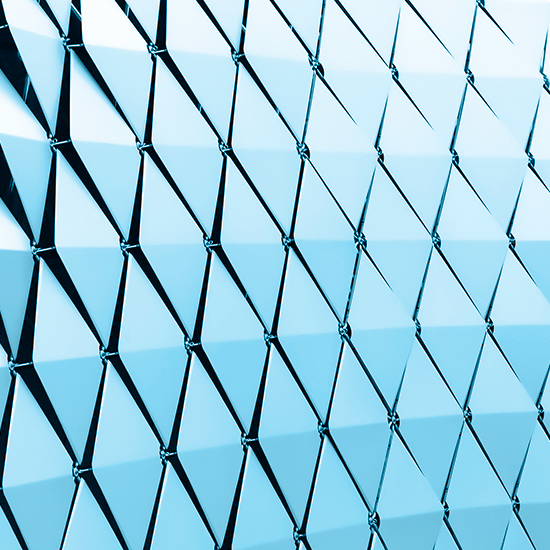
The aluminium coating
Coating of aluminium
- Surface preparation of the coated elements
- Chemical pre-treatment
- Powder or liquid paint coating
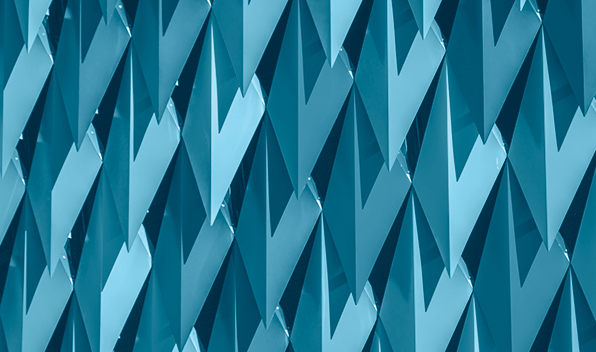

Surface preparation of coated elements
It aims to clean the surface of any kind of contamination, such as dust, lubricating greases etc. and to remove a superficial layer of the profile to eliminate the presence of oxides on the surface of the profile.
In Qualicoat this attack can be of two types:
- Standard qualification: in which the etching rate is 1 g/m2
- Enhanced qualification or SEASIDE: in which the minimum etching rate is 2 g/m2
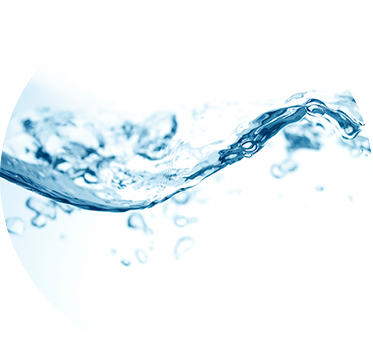
Chemical pretreatment
Its purpose is to prepare the surface for a perfect adhesion of the paint coating and to improve the corrosion behaviour of the element.
It can be of two types:
- Chromic: in this case, a layer of hexavalent chromium is deposited on the surface of the profile with a layer weight of between 0.6 and 1.2 g/m2 (1.5 g/m2 for green chromium).
- Alternative or so-called chrome-free: In these cases, the coating weight depends on the nature of the pretreatment. This process is environmentally friendly or green as it does not contain any pollutants.
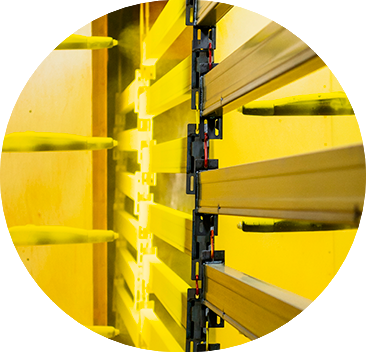
Paint coating
The paint can be:
- Powder paint: with a minimum thickness of 60 µm, this paint is electrostatically deposited on the surface of the profile and then hardened by polymerisation in ovens at temperatures which, depending on the paint to be applied, are around 200ºC. These paints also incorporate the particularity of being environmentally friendly as they do not incorporate any polluting elements.
- Liquid paint: its use is less widespread in our country.
It can also be lacquered to obtain various finishes, the main one being the wood effect, for which a pretreatment must be carried out and then either two coats of powder paint applied (powder on powder) or a layer of powder paint applied and a film paper adhered afterwards (sublimation).
The labels that guarantee the quality of the coating are QUALICOAT and QUALIDECO.
Drawn Wire
Drawn wire is a cold forming process that reduces the cross section of a rod or wire by passing it through a conical hole or die. This process is used to obtain wires with specific diameters, and can be applied to different types of metals and ductile alloys, including aluminum. Its advantages include obtaining wires with high surface quality, dimensional accuracy and improved mechanical properties.
Drawn wire of aluminum is typically performed on drawn machines, which control the speed at which the wire passes through the dies to ensure the desired section reduction. The drawing process may require multiple passes to achieve larger section reductions.
Aluminum, due to its ductility, is a suitable material for drawn wire, and the resulting products, such as wires and rods, have various applications in industry, such as electrical cables, mechanical parts, food industry, wire deformation, steel mills, welding, etc.
A drawn wire machine is mainly composed of:
- A matrix placed in a die, which will vary the section of the aluminum as it passes through it, due to its shape, with an incoming section smaller than the outgoing section.
- A system for applying lubricant to the wire before it enters the die (to facilitate the passage of the material and reduce heating).
- A clamp to hold the wire to the traction system.
- A pulling and coiling system.
Two other important elements are the welding system that joins the beginning of one wire to the end of the previous one, thus achieving a continuous drawn wire process.
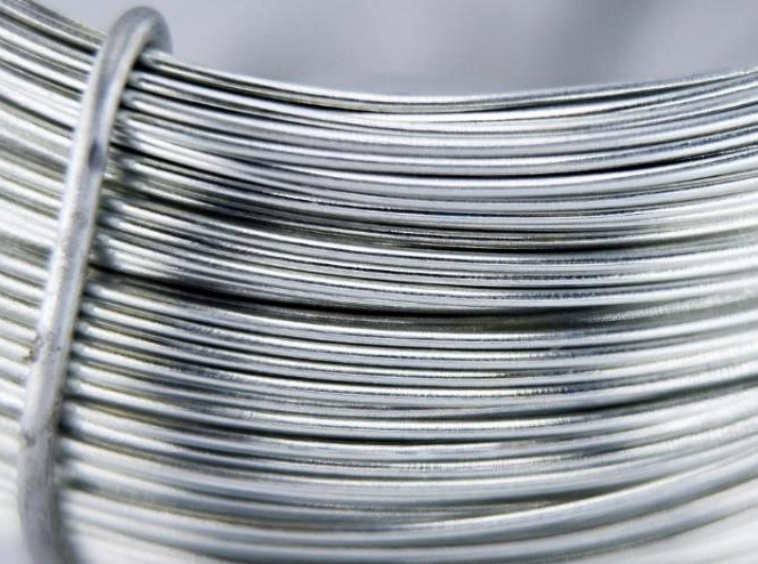